微铸件质量的可靠性直接决定了其工业应用的前景,所以,对微铸件的显微组织和力学性能进行研究是微精密铸造工艺中非常重要的环节。然而,由于微铸件的整体尺寸仅在微米量级,常规的测试手段如单轴拉伸、冲击实验等都不适用,本文作者采用纳米压痕法[8?10]测定微铸件的力学性能。纳米压痕实验是近年来发展起来的针对小载荷、浅压深、微小构件的材料力学性能测试方法,该技术通过具有极高的力分辨率和位移分辨率的纳米硬度计,在压针压入过程中连续获得载荷—压深加载和卸载曲线,利用 OLIVER 和PHARR 方法对加卸载曲线进行数学解析,获得大压深处的载荷 Pmax和接触投影面积 Ac,即可得到材料的纳米硬度和弹性模量值。PETHICA、OLIVER 和PHARR 等[11?13]发展了纳米压痕测试手段,提出了连续刚度测量原理(CSM),利用动态刚度测量,可以在单个压入测试中获得随压入深度连续变化的硬度和模量值,这样就可以研究材料硬度和弹性模量的动态变化过程。
一、实验
1.1 微铸件的制备
微铸件材料为工业上常用的 Zn-Al4 合金,实际化学成分为(质量分数):3.79%Al,0.029%Mg,杂质量<0.2%,其余为 Zn。取成分均匀的 ZnAl 合金铸锭,在中频感应炉中感应熔炼至 460 ℃,降温至 430 ℃时在微铸造成形机上铸造成形,成形微齿轮铸件如图 1所示。其技术指标为:齿顶直径为 600 μm,齿轮轴直径为 300 μm,长 400 μm。由图 1 可见,微齿轮成形良好,轮廓清晰,各部分充型完整。常规尺度铸件试样从微齿轮铸件的浇注系统上截取。
1.2 硬度、模量测试
实验所用的纳米压痕仪为美国 MTS 公司生产的nano indenter XP 型,采用 Berkovich 型压头,系统的载荷分辨率为 50 nN,位移分辨率为 0.01 nm。实验加载过程如下:采用载荷控制模式,加载过程中保持加载速率/载荷( P& / P )恒定,本文取 P& / P =0.05 s?1,直到压深达到 1 000 nm,在大值的位置停留 30 s 以去除蠕变带来的影响[13],然后以相同速率卸载至 10%载荷处,保持 1 min,消除热漂移影响,后完全卸载。压痕形貌由扫描电镜照片给出,分别在微齿轮齿部和轴部的不同位置打点,检验性能差别,每个数据取 3次实验的平均值。
常规尺度铸件试样的硬度值由显微硬度给出。玻士压针和维氏压针的测试结果在理论上是可比的[14],当两者的接触深度相同时,纳米压入硬度和显微硬度理论比值为 1.076。实验中,选用的载荷为 0.5 N,得到的压痕对角线直径为 11.32 μm,换算成深度约为1.06 μm,与压痕实验的压入深度相近。
二、实验结果
图 2 所示为微齿轮铸件齿部和轴部某一压痕点的载荷—压深加卸载曲线,其余各点的加卸载曲线类似。微齿轮齿部的大加载载荷为 24.4 mN,轴部的大载荷为 22.8 mN。微铸件的两部分在大载荷处都表现出了明显的蠕变特性,有关微铸件蠕变特征研究将在后续的文章中作详细介绍。
2.1 微齿轮铸件的纳米硬度
由图 3(b)和图 4(b)可见,在浅压深处硬度值有突兀的变化,这是由于试样表面状况,如表面粗糙度、机械抛光强化层等都会影响材料的硬度测试,所以表层的数据是不准确的,在对实验数据处理时,取压深从 300 nm 到 1 000 nm 时的硬度的平均值。此外,实验过程压痕产生的凸起或者凹陷会影响压痕接触面积的测量精度,从而影响硬度的计算精度,但从图 3(a)和 图 4(a)所示的压痕形貌上看,微铸件压痕未表现出明显的凸起或凹陷。表 1 中的硬度值第 1 列是图 3(b)和图4(b)中硬度的平均值,第2列是大压深1 000 nm处的硬度值。可见,微铸件的硬度随齿顶向齿心的过渡逐渐减小,表现出了明显的梯度性,大为 1.14GPa,小为 0.86 GPa,梯度值可达 1 ?1.32。齿轮轴部分的硬度要小于齿部,这与微齿轮铸件的凝固顺序有关。此外,与常规铸件相比,即使微铸件的小硬度(压痕 4 处)也是常规硬度的 1.3 倍,而齿顶处的硬度值更是达到了常规铸件的 1.7 倍,微铸件的性能得到了极大的提升。
2.2 微齿轮铸件的弹性模量
弹性模量曲线同硬度曲线类似,故也取压深 300nm 到 1 000 nm 时的平均值。此外,弹性模量曲线非常不稳定,呈周期性的波动,且有随压深增加而下降的趋势,文献[15]指出,在纳米压痕实验中,即便对于均匀的单晶材料,其测定的模量值也会随着载荷条件(压入深度)变化而发生变化,原因和材料的均匀程度以及微尺度构件的“尺寸效应”有关。由表 1 中微铸件和常规铸件的弹性模量数据可知,微铸件的弹性模量数值比较分散,并未表现出明显的规律性,齿部和轴部的数值差别不大,都在 55~73 GPa 之间,但与常规尺寸铸件的 130 GPa 相比却显著降低。图 5 给出了不同压点处(与表 1 的顺序相同,横坐标中的 1~9 分别对应齿顶~常规铸件)弹性模量和硬度的分布,从图中可以更为清楚地看到上述的分析结果。
三、分析与讨论
性能的改变往往反应在组织的变化上。众所周知,铸件的散热能力正比于其散热表面积与体积的比值,在微精密铸造条件下,由于微铸件的尺寸微小,使得这个比值可达常规铸件的千倍甚至万倍以上,相应的散热能力也比常规铸件提高成千上万倍。因此,在同等凝固条件下,微铸件的冷却速度极快,约在10?4~10?5数量级,在凝固过程中表现出了强烈的非平衡凝固特征,得到了典型的非平衡凝固组织。
3.1 微齿轮铸件的晶粒尺寸对硬度的影响
图 6 和图 7 分别为常规铸件和微齿轮铸件显微组织的 SEM 像,选择了对比较明显的齿顶和齿心处的微铸件的组织说明。对比图 6、图 7,可发现微铸件的晶粒尺寸明显细化,即使在齿心处也只有宏观组织的1/8 左右,具体值见表 2,且随着从齿顶到齿心过渡(图7(a)~(b)),晶粒尺寸又表现出了逐渐粗化的特征,由齿顶的 4.5 μm 过渡到齿心处的 10.3 μm,齿轮轴是后凝固的部位,所以晶粒尺寸相对较大,与齿心处相似,达到 9.8 μm。
常规状态下材料的硬度对组织形态表现出依赖性,大部分材料都符合 Hall-Petch 公式[1, 17],即随着晶粒尺寸的减小,材料的硬度增加。由此可见,微齿轮铸件组织的细化是硬度提高的主要原因,而齿轮硬度的提升能有效的防止齿轮塑性变形失效。
3.2 微齿轮铸件组织形态对弹性模量的影响
弹性模量是原子间结合力的一种表征,对材料的组织不十分敏感。但对固溶体合金而言,当溶质的原子尺寸较大时会引起合金晶格膨胀,导致合金的弹性模量下降[18]。同时,当溶质元素的原子价高于溶剂元素时,也会导致合金弹性模量的下降[18]。针对本实验中使用的材料 ZnAl4 合金,Zn、Al 原子的半径分别为0.274 0、0.286 0 nm,原子价分别为+2 价、+3 价,所以提高 Al 原子在 Zn 基体中的固溶度或者增加固溶体的数量都会引起材料弹性模量的下降。
对比图 6 与图 7,可发现微齿轮铸件初生 β-Zn 相(图中 A 区和 B 区)的体积分数明显增加。从图 7(a)~(b)可清楚地观察到:在微齿轮铸件的各部位,初生 β-Zn相的数量都极大地增加,尤其是在齿顶处,几乎已达到 90%以上;即使是在数量较少的齿心和轴部 β-Zn相的体积分数也达到了 70%以上,均远大于平衡凝固时的 45%。此外,对初生 β-Zn 相进行 EDS 分析,结果表明在 β-Zn 相中 Al 的质量分数约为 6%左右,远大于平衡凝固时室温下的固溶度。由以上分析可知,快速冷却过程造成的非平衡凝固组织是引起微铸件弹性模量下降的主要原因。
四、结论
1) 微齿轮铸件的硬度优于常规铸件,大提高了约 1.7 倍,且在微齿轮的齿心、齿根及齿尖等不同部位,硬度表现出对晶粒尺寸的依赖性,随着晶粒尺寸的细化,由 0.86 GPa 过渡到 1.14 GPa。
2) 微齿轮铸件的弹性模量低于常规尺寸铸件,只为常规值的一半左右。分析表明,快速冷却引起的初生 β-Zn 相体积分数增加和 Al 在 Zn 中固溶度的增加是主要原因。
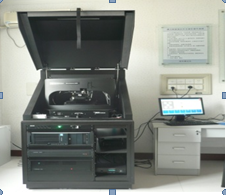